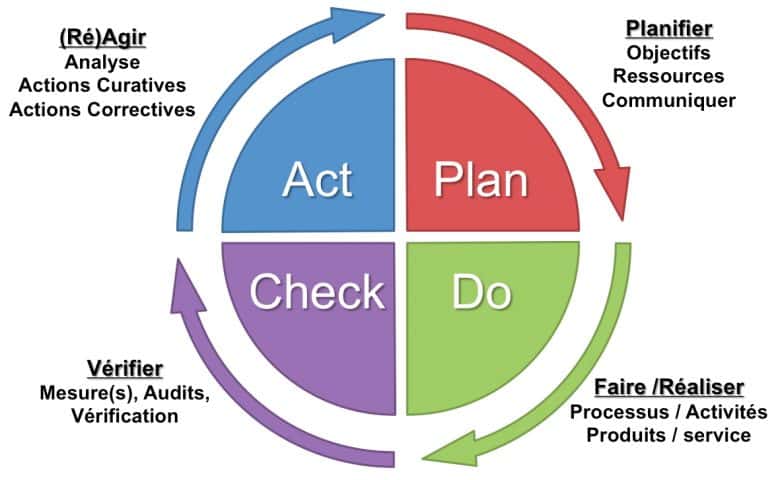
L’amélioration continue dans votre entreprise vise à optimiser les performances de cette dernière en termes de productivité et de gestion efficiente des ressources. Plusieurs méthodes ont vu le jour afin de permettre aux entreprises de connaitre du succès. Nous vous expliquons le bien-fondé de cette démarche et vous proposons quelques méthodes d’améliorations continues qui ont connu du succès.
Qu’est-ce que l’amélioration continue ?
L’amélioration continue permet à l’entreprise de gagner en performance et en qualité. Elle est le 5e pilier de management parmi les 7 principes qui régissent la qualité de la norme ISO 9001. Cette démarche d’amélioration continue doit être un objectif permanent de la firme.
La meilleure représentation de l’amélioration continue est celle de la roue de Deming. L’amélioration continue est en fait un cycle d’actions dont le seul but est l’optimisation des opérations de l’entreprise.
Quels sont les avantages de la mise en place d’un processus d’amélioration continue ?
Il existe plusieurs raisons qui poussent à intégrer ce système de management dans votre entreprise.
L’amélioration continue pour un changement progressif
La mise en place des actions et tâches faciles à réaliser fait partie du processus de l’amélioration continue. En procédant de cette façon, vous atteignez vos objectifs de façon progressive et sans pression.
La méthode du cycle PDCA (Planifier Développer Contrôler Ajuster) est le procédé d’amélioration continue qu’il faut adopter. Il est idéal si vous souhaitez faire des changements sans porter atteinte à l’organisation de l’entreprise. Cette stratégie favorise l’adhésion de la majorité de vos collaborateurs.
L’amélioration continue pour une résolution efficace et prompte des problèmes
Grâce à l’amélioration continue, vous pouvez aisément repérer tous problèmes liés à l’organisation fonctionnelle de votre entreprise. Dès que le problème est identifié, l’entreprise peut trouver des approches de résolution des dysfonctionnements détectés. Ce processus participe à l’amélioration du système organisationnel de la société.
L’amélioration continue pour réduire le gaspillage
Avec l’amélioration continue, vous pouvez détecter tout ce qui s’apparente au gaspillage. En effet, l’amélioration continue permet de supprimer de la chaîne toutes activités qui n’apportent aucune valeur à l’évolution de l’entreprise. Il s’agit entre autres du temps d’attente, de la surproduction, des tâches sans valeur ajoutée, les déplacements, etc.
En supprimant tout ce qui est gaspillage, vous verrez les performances de votre entreprise augmenter en termes de productivité et d’efficacité. Ces suppressions doivent se faire de manière progressive et ne coutent pas grande chose en termes de frais.
L’amélioration continue au service de la motivation des équipes
En optant pour l’amélioration continue dans votre entreprise, vous fédérez vos assistants vers un objectif commun. Ce faisant, ils ont tous une raison de vouloir être efficaces et productifs. Le cycle PDCA s’inscrit dans cette dynamique et aide les managers d’entreprise à trouver la bonne méthode pour motiver leurs employés ou collaborateurs.
L’amélioration continue pour permettre une meilleure visibilité
L’amélioration continue bien appliquée met la lumière sur chaque étape du processus. Il s’agit entre autres de la planification des actions, de leurs réalisations, des résultats obtenus et enfin des actions à réaliser pour corriger les manquements. En mettant au premier plan toutes ces étapes, vous incitez les assistants à être plus productifs et motivés pour réaliser de meilleures performances.
Quelles sont les conditions pour réussir le processus d’amélioration continue dans votre entreprise ?
Le Lean management ou encore amélioration continue étant une démarche visant à optimiser les performances de l’entreprise touche à tous les processus de celle-ci. Pour la bonne marche de ce mode de management, l’implication de tous les acteurs de l’entreprise est requise. Il s’agit de la direction et des assistants.
Le rôle de la direction dans l’accomplissement du Lean management
La direction de l’entreprise à un rôle à jouer afin que l’amélioration continue puisse connaitre du succès. C’est à la direction de l’entreprise que revient la tâche du déploiement de la démarche.
Elle doit par la suite s’assurer que les collaborateurs adhèrent à cette démarche et l’appliquent. Il peut arriver qu’en cas d’absence d’un spécialiste de l’amélioration continue, l’entreprise fasse appel à un manager de transition pour la mise en œuvre de cette démarche.
Le rôle des collaborateurs dans le processus d’amélioration continue.
Les collaborateurs ont leurs partitions à jouer dans le bon fonctionnement du processus d’amélioration continue d’une entreprise. Le premier facteur du succès du Lean management est l’adhésion des collaborateurs. S’ils ne s’identifient pas au changement que la direction propose, la démarche n’aboutira pas.
Il faudrait donc que l’administration arrive à détecter ce qui pourrait créer de la résistance au changement qu’elle se prépare à mettre en place. Pour ce faire, la direction doit présenter le projet et s’assurer que tous ses assistants l’ont compris. Ils doivent percevoir lors de la présentation les raisons de cette démarche d’amélioration continue :
- meilleure performance,
- élimination des tâches inutiles,
- bonne ambiance de travail au sein de l’entreprise,
- sérénité dans le travail,
- cadre de travail convivial, etc.
Une fois que les assistants ont compris leurs rôles et que leurs intérêts sont clairement définis, ils pourront adhérer sans protocole au changement. Dès qu’ils y adhèrent, ils deviendront les acteurs principaux de la firme en recherche perpétuelle de progrès.
Qu’est-ce que le principe du management continue ?
Le principe de l’amélioration continue consiste à créer de la valeur de façon progressive et à réduire les gaspillages au sein de la firme. Ces changements se font sans investissements importants et surtout sans bouleverser l’organisation de l’équipe. Les effets de l’amélioration continue se font ressentir sur le moyen ou le long terme.
L’amélioration continue ne cautionne donc pas le changement radical ou brusque du processus de l’entreprise. Les pratiques ou technologies autrefois employées par l’entreprise doivent connaitre un changement graduel, mais ceci en ayant l’adhésion de tous les collaborateurs.
Quelques méthodes et outils de l’amélioration continue
De la même manière qu’il existe plusieurs types de management, c’est de la même façon qu’il existe plusieurs méthodes d’amélioration continue.
La méthode PDCA
La méthode PDCA (Plan, Do, Check, Act) ou roue de Deming est une démarche de l’amélioration continue qui vise une gestion de qualité. Ce plan facilite le test d’un produit ou service assez rapidement.
Ces nouveaux produits ou services vont connaitre plusieurs ajustements jusqu’à ce que le résultat final attendu soit réel. Cette stratégie pensée par le statisticien William Edward Deming dans les années 50 se décline en 4 étapes cycliques.
- Plan ou planifier : l’entreprise doit prévoir et planifier tout ce qui doit être réalisé en termes de processus et d’activité
- Do ou Déployer : c’est la phase d’expérimentation de la solution choisie
- Check ou Contrôler : c’est la phase de vérification, de suivi et de contrôle des actions menées
- Adjust, Act ou Ajuster : à ce niveau, il faudrait que l’entreprise s’adapte aux différents changements mis en place
La démarche kaizen
Le mot Kaizen d’origine japonaise est décomposé en Kaï qui veut dire <<changement>> et Zen qui veut dire <<meilleur ou vers le meilleur>>. La méthode du Kaizen se base sur la réalisation de petites améliorations de façon continue et graduelle.
En procédant de façon progressive, l’entreprise a de fortes chances de voir ses collaborateurs adhérer au changement proposé. D’autres spécialistes ne considèrent pas le Kaizen comme une méthode d’amélioration continue. Ils stipulent que c’est plutôt un état d’esprit.
La méthode 5s
Les usines de Toyota furent les premières à expérimenter la méthode des 5 S afin d’optimiser leur production. Cette méthode vise à optimiser l’espace de travail et améliorer l’environnement de travail des assistants. Elle se décline en 5 étapes que voici :
- Serei (Débarrasser) : se débarrasser du superflu, jeter ce qui n’est pas régulièrement utilisé et qui parait inutile
- Seiton (Ranger) : ranger l’espace de travail, classer et ordonner afin d’avoir chaque chose à sa place
- Seiso (Nettoyer) : nettoyer l’espace de travail et les outils de production pour éviter les dysfonctionnements et améliorer la sécurité
- Seiketsu (Maintenir l’ordre) : une fois que le superflu est jeté, que l’espace de travail est rangé, classé et ordonné, il faut continuer à maintenir l’ordre
- Shitsuke (Être rigoureux) : pour être efficace, il est important de continuer à respecter les 4 S précédents de manière rigoureuse et durable
Si cette méthode est bien appliquée, les assistants pourront travailler dans un espace optimisé, serein et sans danger. Ils pourront retrouver aisément les informations puisque tout est rangé à sa place.
De cette façon, ils pourront gagner en efficacité puisque les documents seront facilement trouvables. Le taux des accidents de travail va connaitre aussi une baisse drastique.
La méthode six sigma
Motorola est l’entreprise qui a inventé la méthode Six Sigma en 1986 dans le but d’améliorer la qualité de production. Cette qualité de production qui vise zéro défaut doit se faire en optimisant les processus de l’entreprise. 5 étapes cycliques caractérisent cette méthode.
Définir
Au niveau de cette étape, vous devrez définir les besoins du client et soulever les problèmes à résoudre. Procédez à une étude qualitative afin de comprendre les besoins du client, ses motivations et ses comportements.
Mesurer
L’entreprise durant cette étape doit évaluer la performance du processus actuel. Pour ce faire, elle doit procéder à la collecte des données afin de réaliser des études quantitatives. Un exemple d’étude à réaliser est celui de la satisfaction des clients. Les résultats recueillis vont servir à mesurer la performance du processus.
Analyser
Une fois les données collectées, elles seront analysées. Elles serviront ensuite de repère pour la proposition d’opérations d’amélioration.
Améliorer
Cette étape est celle de la mise en application des propositions de solution. Ainsi, l’entreprise verra les problèmes se résoudre et son processus s’améliorer.
Contrôler
Cette étape est celle du suivi afin de s’assurer que les solutions mises en application sont réellement ce qu’il faut pour l’entreprise et les clients. Ils doivent donc mettre en application un plan de surveillance et disposer de données mesurables.
La méthode « juste à temps »
La méthode du juste à temps est essentiellement utilisée pour une meilleure gestion des approvisionnements. Avec cette méthode, l’approvisionnement des matières premières ou tout autre élément ne se fait qu’à la réception des commandes clients. Ceci permet l’élimination des stocks inutiles et met un coup de frein au gaspillage.
Les principaux acteurs de la bonne marche de cette méthode sont les clients et les fournisseurs. L’entreprise quant à elle doit chercher à optimiser son stock en faisant par exemple une faible estimation des besoins de production. Ils doivent aussi privilégier un approvisionnement local afin de réduire les délais et les coûts. Une gestion stricte des stocks et des commandes est recommandée.
Les cercles de qualité
Cette méthode de travail tire ses origines du Japon et vise la résolution des problèmes au sein de l’entreprise. Elle consiste à faire des réunions de façon périodique avec les personnes directement concernées par la problématique à résoudre. Ces personnes étant les mieux placées pour comprendre le problème pourront donc analyser, diagnostiquer et proposer des solutions objectives.
Cette méthode est collaborative et participative. Les collaborateurs pourront se sentir importants au sein de l’entreprise. Les solutions proposées vont favoriser l’augmentation de la productivité et réduire les gaspillages dans l’entreprise. Une meilleure communication va s’installer et les collaborateurs seront mieux motivés pour l’atteinte des objectifs.
Ces séances de travail vont permettre aux assistants de faire des échanges d’expériences. Ils pourront proposer des idées innovantes et des propositions de formation peuvent en découler. Cette méthode d’amélioration continue connait généralement une forte adhésion des collaborateurs au processus de changement.
En définitive, il en ressort que la démarche d’amélioration continue est un procédé nécessaire pour toute entreprise qui vise l’excellence. Compter sur le bon sens des collaborateurs et bâcler ce processus s’avère être une erreur monumentale.